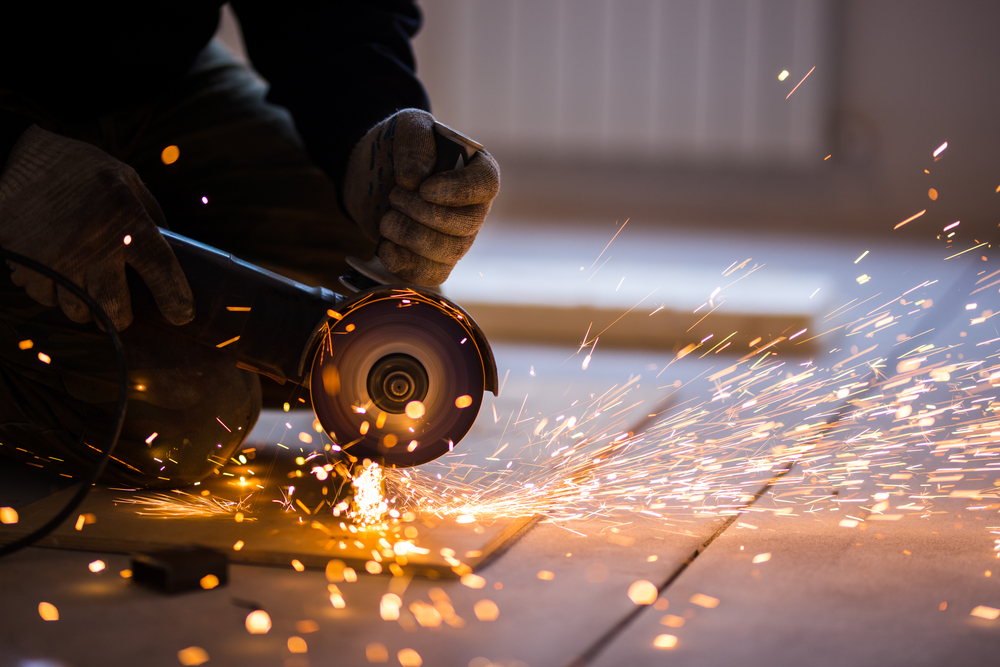
How Extreme Cold Affects Cutting Blade Performance in Alaska
February 24, 2025 9:02 pm Leave your thoughtsAlaska is known for its breathtaking landscapes, but it also presents extreme weather challenges that impact various industries. One of the biggest concerns for professionals working in frigid conditions is how their tools perform under subzero temperatures. Cutting blades, whether used for industrial applications, woodworking, or ice-cutting, can experience severe performance degradation when exposed to the extreme cold of an Alaskan winter. The best cutting blades for subzero temperatures must be designed to withstand brittle fractures, reduced flexibility, and increased resistance when slicing through materials. Without the proper blade composition and maintenance, efficiency can drop dramatically, and costs can soar due to frequent replacements.
Understanding the science behind how extreme cold affects metal is crucial. At subzero temperatures, the molecular structure of steel and other blade materials becomes more rigid, making them susceptible to chipping and breaking. Many standard cutting blades are designed for moderate climates, and when used in freezing conditions, they can quickly lose their sharpness and structural integrity. The best approach to mitigating these risks is selecting high-quality materials that retain their properties even in freezing conditions. Blades with high carbon content, cryogenically treated metals, and specific coatings help improve longevity and prevent sudden failures in the field.
The Challenges of Cutting in Alaska’s Harsh Winters
Working in Alaska’s severe winter conditions introduces several challenges that can significantly impact cutting blade performance. One major issue is that most materials become harder when exposed to extreme cold. Wood, plastic, and even metal exhibit different structural behaviors at freezing temperatures, requiring blades with enhanced durability to cope with these shifts. As temperatures plummet, materials become less pliable, making cutting tasks more strenuous and leading to accelerated blade wear. Preventing blade wear in freezing conditions in Alaska requires careful selection of tools, proper handling, and ongoing maintenance to ensure optimal performance.
Another challenge that many professionals face is the impact of freezing temperatures on lubrication. Many cutting blades require some form of lubrication to function effectively. However, in extreme cold, standard lubricants thicken or freeze, leading to increased friction and reduced cutting efficiency. Special cold-weather lubricants are necessary to counteract this issue, ensuring that blades continue to operate smoothly even in subzero environments. Additionally, when cutting through ice or snow-packed materials, ice buildup on the blade can further reduce efficiency, forcing workers to take extra precautions to prevent operational slowdowns.
Choosing the Right Blades for Freezing Conditions
Selecting the best cutting blades for subzero temperatures requires an understanding of material composition, coatings, and design. High-speed steel (HSS) blades are known for their resilience, but in subzero conditions, they may still become brittle. Tungsten carbide blades, on the other hand, provide enhanced durability and maintain sharpness longer in freezing temperatures. Additionally, cryogenically treated blades are gaining popularity in Alaska due to their improved molecular structure, which enhances their resistance to extreme cold.
Coatings also play a crucial role in blade performance. Titanium or diamond-like coatings can significantly enhance a blade’s ability to cut through tough materials without succumbing to rapid wear. These coatings reduce friction, allowing the blade to maintain a consistent cutting motion even in extreme conditions. Professionals working in Alaska also benefit from serrated or specialized tooth patterns that help distribute cutting forces more evenly, preventing premature dulling and breakage.
Beyond material composition, it is essential to consider blade flexibility. While some rigid blades provide precise cuts, they may be prone to cracking when exposed to extreme cold. A balanced approach involves selecting blades that offer a combination of hardness and elasticity, ensuring they can withstand impact without fracturing. Investing in blades specifically designed for freezing conditions ensures consistent performance, fewer replacements, and lower overall costs in the long run.
Preventing Blade Wear and Ensuring Longevity
Preventing blade wear in freezing conditions in Alaska involves a combination of proper storage, maintenance, and handling. Storing blades in temperature-controlled environments before use helps prevent them from becoming overly brittle when first exposed to freezing temperatures. Warming up blades gradually before heavy-duty use can also minimize the risk of sudden fractures. When blades are not in use, proper storage in dry, insulated cases helps reduce moisture exposure, preventing rust or corrosion that can weaken the blade structure.
Regular maintenance is another critical factor in ensuring longevity. After each use, cleaning blades thoroughly to remove debris, ice buildup, and residue can prevent long-term damage. Applying cold-weather lubricants before and after use reduces friction and helps maintain smooth cutting action. Routine inspections for cracks or dull edges allow professionals to replace blades before they become hazardous or inefficient. Sharpening blades with the appropriate tools designed for extreme cold use ensures that they remain effective over time.
Handling techniques also play a vital role in blade preservation. Using steady, consistent pressure instead of forcing a cut helps reduce stress on the blade. When cutting through dense materials, allowing the blade to do the work rather than applying excessive force minimizes the chances of chipping or breakage. Professionals working in Alaska often adopt specialized cutting techniques to adapt to the harsh climate, ensuring that tools perform optimally despite challenging conditions.
Industry Applications and the Future of Cold-Resistant Cutting Technology
The need for cutting blades that perform well in extreme cold extends across multiple industries in Alaska. From logging and construction to ice carving and industrial metalwork, professionals rely on high-performance blades to complete their tasks efficiently. In logging operations, cutting through frozen timber requires blades that resist dulling while maintaining precision. In construction, working with frozen concrete or metal demands specialized blades that can endure high-stress conditions without compromising performance.
Ice sculptors, a niche yet vital industry in Alaska, rely on precision cutting tools to carve intricate designs from large ice blocks. The best cutting blades for subzero temperatures enable artists to work with greater accuracy and prevent cracking or chipping that can ruin their sculptures. Similarly, industries involved in ice road construction or pipeline maintenance in Alaska require blades capable of cutting through thick ice or permafrost while maintaining stability and sharpness.
Looking ahead, advancements in cold-resistant cutting technology continue to evolve. Researchers and manufacturers are developing new blade compositions that integrate nanomaterials to enhance strength and flexibility in extreme conditions. Improved coatings, self-lubricating blades, and hybrid materials designed specifically for subzero environments are expected to enhance performance and longevity. As industries in Alaska continue to grow, the demand for cutting blades that can withstand harsh winters will drive innovation in blade design and material science, ensuring that professionals have the tools they need to succeed in freezing temperatures.
Conclusion
Extreme cold poses unique challenges for cutting blade performance, but with the right materials, maintenance, and handling techniques, professionals working in Alaska can ensure their tools remain efficient and reliable. Investing in the best cutting blades for subzero temperatures and implementing preventative measures against blade wear will lead to improved efficiency, reduced costs, and a longer lifespan for cutting tools in the harshest environments.
Got questions about cutting blades? Let us help! Call us today to learn more!
Categorised in: Metal Cutting Blades
This post was written by admin