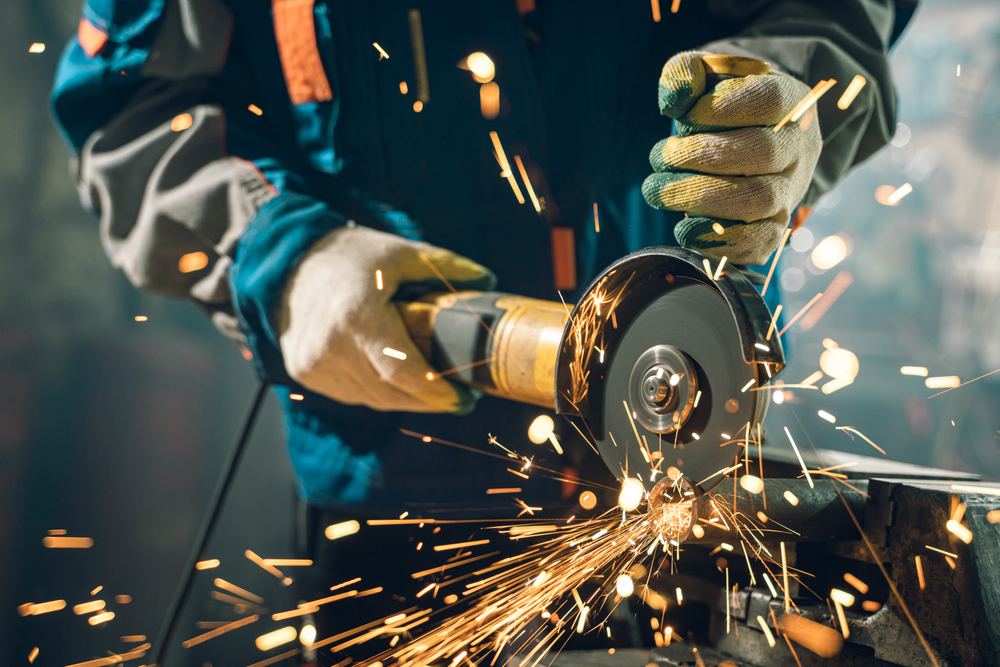
The Challenges of Industrial Cutting in Remote Locations: Insights from Alaska
February 12, 2025 9:02 pm Leave your thoughtsAlaska, with its rugged terrain and unpredictable weather, presents unique challenges for industries that rely on heavy-duty cutting blades for extreme conditions of Alaska. The state’s vast wilderness, harsh winters, and isolated work sites create significant operational obstacles that demand specialized equipment and expertise. The remote nature of many industrial projects, whether in logging, mining, or infrastructure development, requires precision and durability in every tool used. Industrial cutting blades in Alaska must withstand freezing temperatures, heavy snow, and difficult-to-access sites, making the selection of materials and blade design crucial for efficiency and effectiveness.
The environmental factors in Alaska also contribute to accelerated wear and tear on cutting equipment. The sub-zero temperatures can cause metal fatigue, while wet and icy conditions increase the risk of corrosion. Additionally, unpredictable weather patterns, including heavy snowfall and ice storms, can lead to delays and impact the efficiency of industrial operations. Workers must ensure that their cutting tools are designed to handle such extreme conditions to maintain productivity and prevent costly downtimes. Companies operating in Alaska must carefully select cutting blades that offer superior performance under these harsh environmental conditions.
The Importance of Durability and Performance in Cutting Equipment
In the remote industrial sites of Alaska, durability is a top priority. The industrial cutting blades in Alaska must be built with high-strength alloys and advanced coatings to resist wear and damage. Standard blades often fail under such demanding conditions, leading to increased downtime and higher maintenance costs. Companies in the logging, mining, and construction industries require blades that not only perform consistently but also maintain their sharpness and structural integrity over extended periods.
Performance is also a key consideration when selecting heavy-duty cutting blades for extreme conditions of Alaska. The ability of a blade to maintain a sharp edge while cutting through frozen wood, rock, and other tough materials is critical. High-carbon steel and tungsten carbide are commonly used materials that provide the necessary hardness and resistance to impact. Additionally, blades designed with reinforced edges and special coatings can reduce friction and prevent overheating, which is essential for operations in extreme cold. Ensuring that blades can handle these rigorous demands allows companies to maximize their efficiency and minimize operational disruptions.
One of the greatest challenges of working with industrial cutting blades in Alaska is the difficulty in obtaining replacement parts. Given the remote nature of many worksites, access to maintenance facilities and spare blades is often limited. This means that companies must invest in long-lasting, high-performance blades that can withstand extended use without frequent replacements. The ability to continue operations without constant blade failures is crucial for maintaining productivity in Alaska’s harsh industrial landscape.
Logistical Challenges and Maintenance in Remote Locations
Transportation of equipment and supplies is a significant hurdle in Alaska’s industrial sector. Many remote locations are only accessible by air, boat, or seasonal ice roads, which makes delivering industrial cutting blades in Alaska a logistical challenge. Due to these constraints, companies must plan their operations meticulously to ensure that all necessary tools and spare parts are available on-site before work begins. Any delay in obtaining replacement blades or maintenance tools can lead to costly downtime and project setbacks.
The extreme weather conditions also impact the maintenance and storage of heavy-duty cutting blades for extreme conditions of Alaska. Sub-zero temperatures can cause metal components to contract and become brittle, increasing the likelihood of breakage. Ice buildup on equipment can further hinder performance, requiring workers to conduct regular inspections and preventive maintenance. Industrial teams operating in remote areas must be trained in proper blade care, including sharpening techniques, lubrication methods, and storage solutions to prolong the life of their cutting equipment.
In addition to weather-related challenges, remote worksites often lack access to specialized repair services. This necessitates on-site maintenance capabilities, with workers trained in diagnosing and repairing blade issues. Investing in multi-purpose cutting blades that can handle a variety of materials can also help reduce the need for multiple types of blades, simplifying logistics and maintenance efforts. Companies must balance the need for durability and efficiency with the practical limitations of operating in Alaska’s remote industrial sites.
Safety Considerations for Industrial Cutting in Alaska
Ensuring worker safety is paramount in any industrial setting, but it becomes even more critical in Alaska’s remote locations. The combination of extreme weather, isolated worksites, and heavy-duty equipment creates an environment where safety precautions must be rigorously followed. Industrial cutting blades in Alaska must be handled with care, as improper use can lead to serious injuries. Workers must be trained in proper cutting techniques, blade handling, and emergency response protocols to mitigate risks.
One of the primary safety concerns is blade failure due to cold-induced brittleness. When exposed to freezing temperatures, metal can become more prone to cracking or chipping, which can result in dangerous flying debris. To minimize these risks, companies should use heavy-duty cutting blades for extreme conditions of Alaska that are specifically designed to resist temperature-related stress. Additionally, using protective gear such as cut-resistant gloves, face shields, and reinforced clothing can help safeguard workers from potential accidents.
Proper storage and transport of industrial cutting blades are also essential for maintaining safety in remote worksites. Blades should be stored in insulated, moisture-resistant containers to prevent rust and corrosion. When transporting cutting equipment across rough terrain, securing the blades to prevent movement and impact damage is crucial. Workers should also be educated on safe handling practices, including the correct procedures for blade installation, removal, and disposal. By prioritizing safety measures, companies can protect their workforce while maintaining high productivity levels in Alaska’s challenging industrial environments.
Advancements in Cutting Technology for Remote Industrial Applications
As industries in Alaska continue to expand, advancements in cutting technology are helping to overcome many of the challenges associated with remote industrial operations. The development of high-performance materials, such as composite metal alloys and diamond-tipped blades, has significantly improved the durability and efficiency of industrial cutting blades in Alaska. These innovations allow blades to maintain their sharpness for longer periods, reducing the frequency of replacements and maintenance.
Another technological advancement is the integration of automated and remote-controlled cutting systems. These systems enable operators to control cutting equipment from a safe distance, reducing exposure to hazardous conditions. Remote monitoring technology can also provide real-time data on blade performance, allowing workers to detect signs of wear and address maintenance needs before failures occur. By leveraging these technological advancements, companies can enhance both efficiency and safety in their industrial cutting operations.
Additionally, manufacturers are developing blades with specialized coatings and treatments that improve resistance to corrosion and abrasion. These coatings help blades withstand the harsh environmental conditions found in Alaska’s remote locations, extending their lifespan and improving overall performance. The use of eco-friendly lubricants and anti-freeze treatments further enhances blade efficiency while reducing the environmental impact of industrial operations.
As demand for industrial cutting blades in Alaska continues to grow, companies must stay informed about the latest developments in cutting technology. Investing in advanced cutting solutions tailored for extreme conditions can provide a competitive edge, ensuring that operations remain efficient and cost-effective despite the challenges of working in remote locations. By adopting cutting-edge technology, industries operating in Alaska can improve their productivity while minimizing the risks associated with harsh environmental conditions.
Conclusion
Industrial cutting in remote areas like Alaska requires specialized equipment that can withstand extreme weather and challenging logistics. Heavy-duty cutting blades for extreme conditions of Alaska must be durable, high-performing, and resistant to environmental stressors. Companies must navigate logistical challenges, prioritize safety measures, and invest in advanced technology to optimize their operations. By understanding and addressing these challenges, industries can continue to thrive in Alaska’s demanding industrial landscape.
Got questions about cutting blades? Let us help! Call us today to learn more!
Categorised in: Metal Cutting Blades
This post was written by admin